Lean Ford: Revolutionizing Automotive Efficiency And Innovation
Lean Ford represents a transformative approach in the automotive industry, emphasizing efficiency, innovation, and customer-centric solutions. In an era where sustainability and operational excellence are paramount, Ford's lean manufacturing strategies have become a benchmark for global manufacturers. This article delves into the core principles of Lean Ford, its historical evolution, and its impact on modern automotive production.
Lean manufacturing has long been synonymous with Toyota, but Ford's adaptation of lean principles has created a unique framework that aligns with its century-long legacy of innovation. By integrating lean methodologies into its operations, Ford has not only optimized its production processes but also enhanced its product quality and customer satisfaction. This approach has positioned Ford as a leader in sustainable manufacturing practices.
As we explore the Lean Ford philosophy, we will uncover its historical roots, practical applications, and future implications. This article aims to provide a comprehensive understanding of how Ford has successfully implemented lean principles while maintaining its commitment to quality and innovation. Whether you're a manufacturing professional, an automotive enthusiast, or simply curious about lean methodologies, this article offers valuable insights into one of the most impactful strategies in modern industry.
Read also:Melissa Mcknight Unveiling The Talented Actress And Her Remarkable Journey
Table of Contents
- Introduction to Lean Ford
- Historical Evolution of Lean Ford
- Core Principles of Lean Ford
- Implementation of Lean Ford
- Benefits of Lean Ford
- Challenges in Adopting Lean Ford
- Case Studies of Lean Ford Success
- Role of Technology in Lean Ford
- Future of Lean Ford
- Conclusion and Call to Action
Introduction to Lean Ford
Lean Ford is a strategic framework that combines traditional lean manufacturing principles with Ford's innovative approach to automotive production. The concept focuses on eliminating waste, improving process efficiency, and enhancing product quality. By adopting lean methodologies, Ford has been able to streamline its operations, reduce costs, and deliver superior value to customers.
At the heart of Lean Ford lies a commitment to continuous improvement, known as Kaizen. This philosophy encourages employees at all levels to identify inefficiencies and propose solutions, fostering a culture of innovation and collaboration. The result is a manufacturing process that is not only efficient but also adaptable to changing market demands.
Why Lean Ford Matters
The significance of Lean Ford extends beyond cost savings. It represents a holistic approach to manufacturing that prioritizes sustainability, quality, and customer satisfaction. By aligning its operations with lean principles, Ford has set a new standard for the automotive industry, demonstrating that efficiency and innovation can coexist.
Historical Evolution of Lean Ford
The journey of Lean Ford began in the early 20th century with Henry Ford's introduction of the assembly line. While the concept of lean manufacturing was later popularized by Toyota, Ford's pioneering efforts laid the groundwork for modern production systems. Over the decades, Ford has continuously evolved its manufacturing processes, incorporating lean principles to enhance efficiency and quality.
Key Milestones in Lean Ford Development
- 1913: Introduction of the moving assembly line, revolutionizing mass production.
- 1980s: Adoption of Just-In-Time (JIT) principles to reduce inventory costs.
- 2000s: Integration of Six Sigma methodologies to improve process control.
- 2010s: Expansion of lean initiatives across global manufacturing facilities.
Core Principles of Lean Ford
The foundation of Lean Ford rests on five core principles: value, value stream, flow, pull, and perfection. These principles guide every aspect of Ford's manufacturing operations, ensuring that resources are utilized efficiently and customer needs are met effectively.
Understanding the Five Core Principles
Value focuses on identifying what customers truly need and delivering it through efficient processes. The value stream maps all activities required to bring a product from concept to delivery, enabling the identification and elimination of waste. Flow ensures that production processes are smooth and uninterrupted, while pull ensures that products are produced only when needed. Finally, perfection represents the pursuit of continuous improvement, driving innovation and excellence.
Read also:Dave Clark Net Worth The Rise Of An Amazon Legend
Implementation of Lean Ford
Implementing Lean Ford requires a structured approach that involves training, process redesign, and cultural transformation. Ford has invested heavily in educating its workforce about lean principles, ensuring that every employee understands their role in driving efficiency and innovation.
Steps in Implementing Lean Ford
- Conducting a thorough assessment of current processes to identify areas for improvement.
- Training employees in lean methodologies and tools.
- Redesigning processes to eliminate waste and improve flow.
- Monitoring performance metrics to measure the effectiveness of lean initiatives.
Benefits of Lean Ford
The adoption of Lean Ford has yielded numerous benefits for the company, including reduced costs, improved quality, and increased customer satisfaction. By eliminating waste and streamlining processes, Ford has been able to deliver products faster and more efficiently, enhancing its competitive position in the global market.
Key Benefits of Lean Ford
- Cost Reduction: Lean initiatives have significantly reduced production costs by minimizing waste and improving resource utilization.
- Quality Improvement: Enhanced process control and employee involvement have led to higher product quality and fewer defects.
- Customer Satisfaction: Faster delivery times and improved product quality have resulted in higher customer satisfaction levels.
Challenges in Adopting Lean Ford
While the benefits of Lean Ford are substantial, its implementation is not without challenges. Resistance to change, lack of employee engagement, and initial investment costs can hinder the successful adoption of lean principles. Ford has addressed these challenges through effective communication, comprehensive training programs, and a commitment to long-term gains.
Overcoming Implementation Challenges
By fostering a culture of collaboration and innovation, Ford has successfully overcome many of the challenges associated with lean implementation. Employee engagement initiatives, such as suggestion programs and recognition systems, have played a crucial role in driving acceptance and participation in lean activities.
Case Studies of Lean Ford Success
Several case studies highlight the success of Lean Ford in improving operational efficiency and driving innovation. For example, Ford's assembly plant in Michigan achieved significant cost savings and quality improvements through the implementation of lean principles. Similarly, the introduction of lean methodologies at Ford's international facilities has resulted in enhanced productivity and customer satisfaction.
Michigan Assembly Plant Case Study
The Michigan Assembly Plant serves as a prime example of Lean Ford's success. By implementing lean principles, the plant reduced production time by 20% and achieved a 30% reduction in defects. These improvements were driven by employee involvement, process redesign, and the use of advanced technologies.
Role of Technology in Lean Ford
Technology plays a critical role in the success of Lean Ford. Advanced analytics, automation, and digital tools enable real-time monitoring of production processes, facilitating the identification and resolution of inefficiencies. Ford's investment in technology has enhanced its ability to implement lean principles effectively, driving innovation and efficiency across its operations.
Key Technologies Supporting Lean Ford
- Internet of Things (IoT): Enables real-time monitoring of equipment and processes.
- Artificial Intelligence (AI): Facilitates predictive maintenance and process optimization.
- Blockchain: Ensures transparency and traceability in supply chain operations.
Future of Lean Ford
The future of Lean Ford looks promising, with ongoing advancements in technology and a growing emphasis on sustainability. As Ford continues to innovate, it is likely that lean principles will evolve to incorporate emerging technologies and address new challenges in the automotive industry. The company's commitment to continuous improvement ensures that Lean Ford will remain a cornerstone of its manufacturing strategy.
Trends Shaping the Future of Lean Ford
- Increased adoption of Industry 4.0 technologies.
- Greater focus on sustainability and environmental responsibility.
- Expansion of lean initiatives to include service and support operations.
Conclusion and Call to Action
Lean Ford represents a powerful approach to manufacturing that combines efficiency, innovation, and customer-centric solutions. By embracing lean principles, Ford has not only optimized its operations but also enhanced its reputation as a leader in the automotive industry. As the industry continues to evolve, the principles of Lean Ford will remain essential for achieving success in a competitive global market.
We invite you to share your thoughts and experiences with Lean Ford in the comments section below. Your feedback and insights will help us continue to improve and expand our understanding of this transformative approach. Additionally, we encourage you to explore other articles on our site for more insights into lean manufacturing and its applications across various industries.
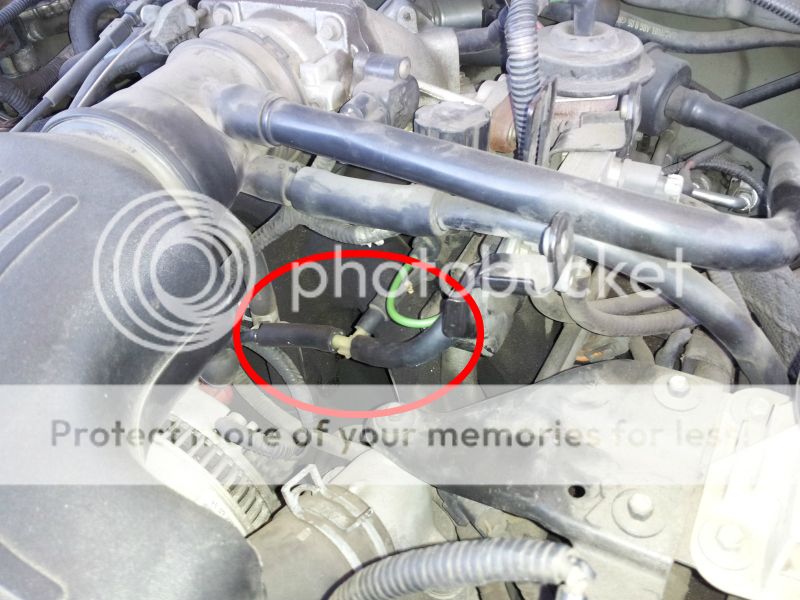
